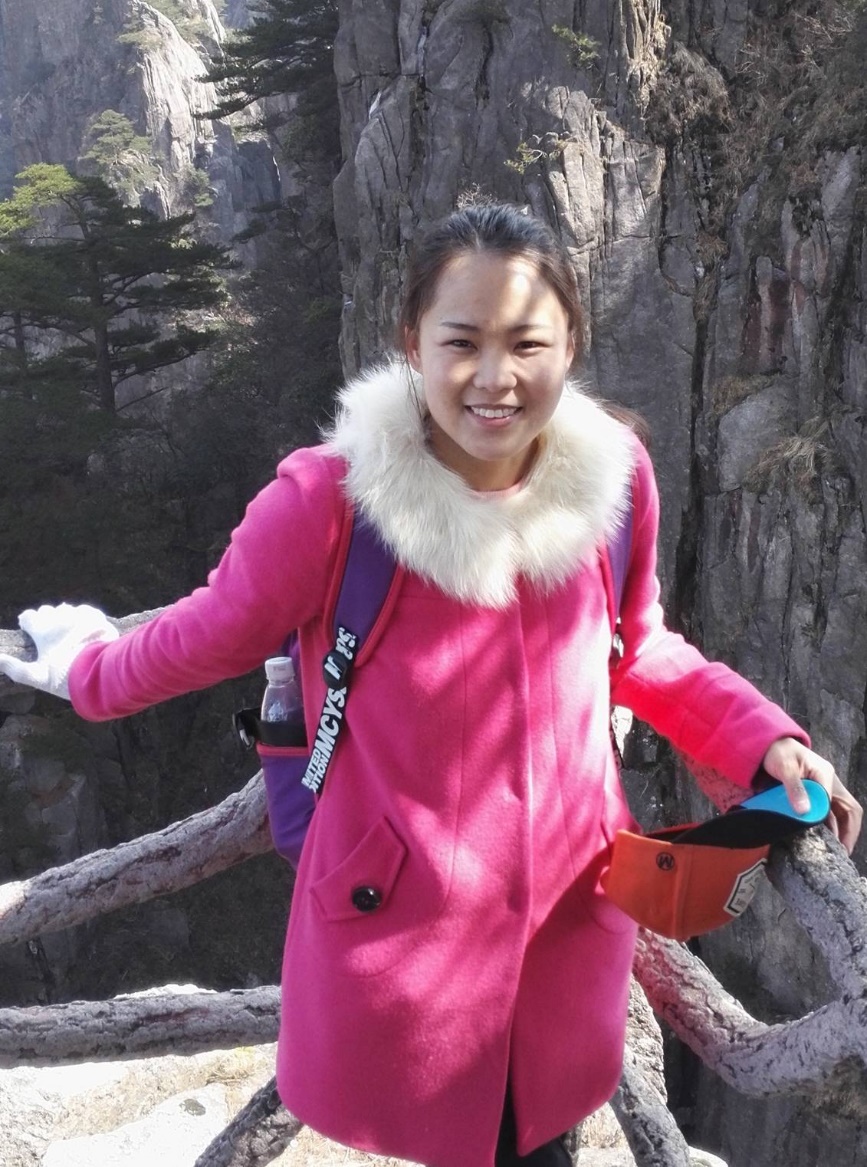
刘霞
论文题目
可控摩擦辅助喷射电沉积薄膜制备技术研究
主要研究
1、提出了可控摩擦辅助喷射电沉积技术,构建了试验系统,解决了传统喷射电沉积技术无法在大电流密度下制备高质量膜层的问题;
2、研究石墨基体可控摩擦辅助喷射电沉积改善镀层表面质量、提高沉积效率的机理,通过单因素试验确定最佳滚压力5.2N,阴极扫面速度860mm/min作为试验参数,极限电流密度达到200A/dm2,是常规喷射电沉积的1.54倍;
3、研究了钕铁硼基体可控摩擦技术改善镀层与基体间结合强度的机理,通过正交试验确定了最佳工艺参数滚压力3.1N,沉积时间10min,电镀液温度50℃,膜基结合力提高到常规方法的1.6倍。
发表论文
[1] Liu Xia, Shen Lida, Qiu Mingbo, Tian Zongjun, Wang Yihao, Zhao Kailin. Jet electrodeposition of nanocrystalline nickel assisted by controllable friction. Surface and Coatings Technology, 2016, 305: 231-240.(已录用)
[2] Wang Yihao, Shen Lida, Qiu Mingbo, Tian Zongjun, Liu Xia, Zhuo Wei. Jet Electrodeposition of Ni-SiO2 Nanocomposite Coatings with Online Friction and Its Performance. Journal of The Electrochemical Society, 2016, 163 (10): D579-D584.(已录用)
[3] Shen Lida, Wang Yihao, Jiang Wei, Liu Xia, Wang Chuan, Tian Zongjun. Jet Electrodeposition Multilayer Nickel On The Surface of Sintered NdFeB and Corrosion Behaviors. Corrosion Engineering Science and Technology, 2016.(已录用)
工作单位
森萨塔科技(常州)有限公司(江苏常州)
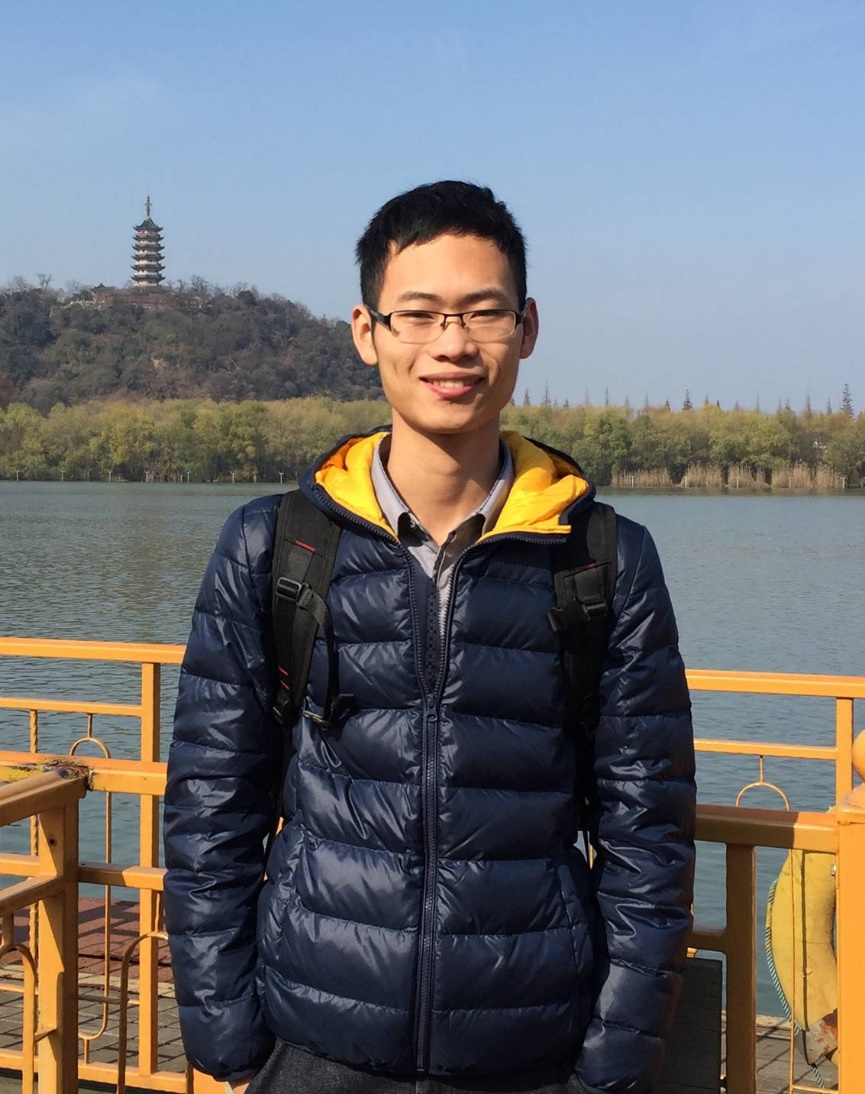
汪轶豪
论文题目
喷射电沉积镍基纳米复合镀层试验研究
主要研究
1、设计并构建了双槽与单槽电沉积实验系统;
2、分析了复合镀层的防腐机理、纳米粒子增强机理,提出了采用陶瓷棒辅助滚压摩擦镀层提高质量的方法;
3、制备了亮镍和暗镍交替沉积的纳米多层膜,与同等厚度的单层结构镀层相比,具有更好的耐腐蚀性能和表面质量;
4、进行了复合镀层制备工艺试验,加入纳米粒子后镀层硬度由550HV增加到627HV,引入滚压摩擦后进一步提高到711HV,并且镀层耐腐蚀性得到进一步提高。
发表论文
[1] Yihao Wang, Lida Shen, Mingbo Qiu, et al. Jet Electrodeposition of Ni-SiO2 Nanocomposite Coatings with Online Friction and Its Performance[J]. Journal of The Electrochemical Society, 2016,163 (10): D579-D584.(SCI已录用 IF 3.012)
[2] Lida Shen, Yihao Wang, Wei Jiang, et al. Jet Electrodeposition Multilayer Nickel On The Surface of Sintered NdFeB and Corrosion Behaviors[J]. Corrosion Engineering Science and Technology, 2016.(SCI已录用)
[3] Liu Xia, Shen Lida, Qiu Mingbo, Tian Zongjun, Wang Yihao, Zhao Kailin. Jet electrodeposition of nanocrystalline nickel assisted by controllable friction. Surface and Coatings Technology,2016.(SCI已录用)
工作单位
远景能源江苏有限公司(江苏无锡)
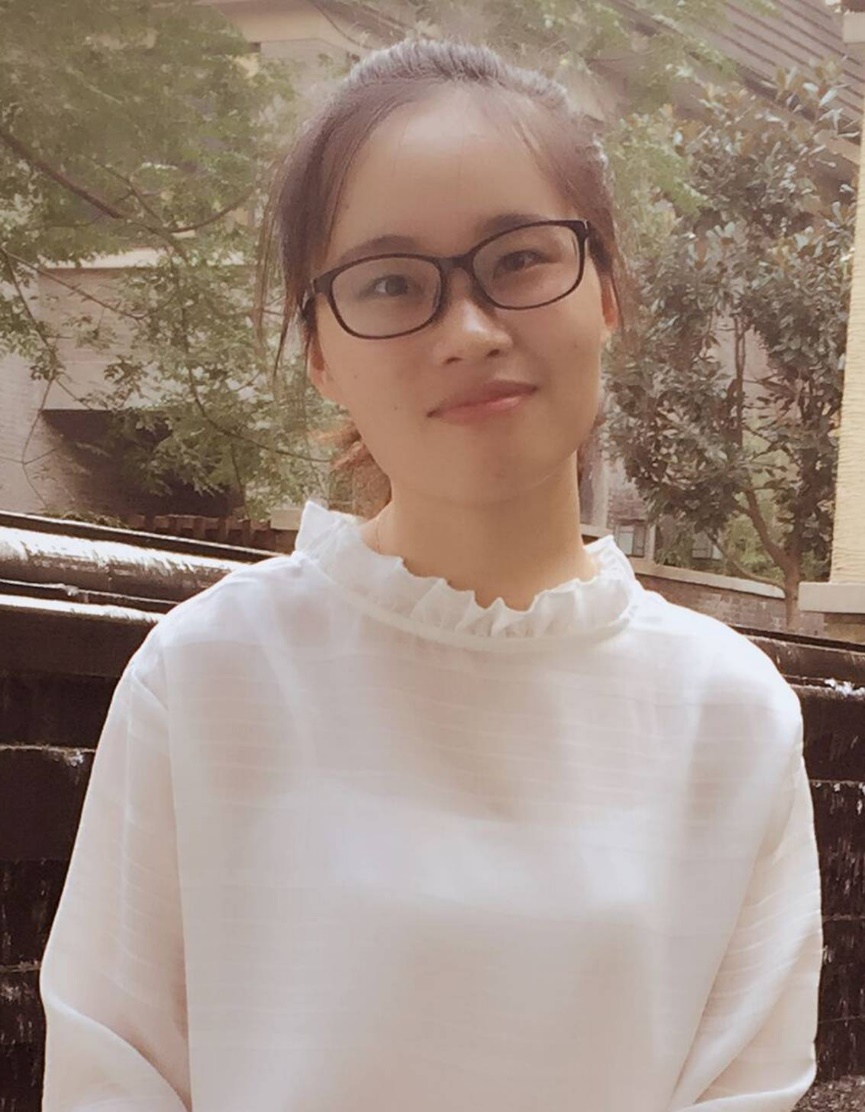
林菡琳
论文题目
毛细管辅助微细电沉积制备金属结构试验研究
主要研究
1、提出了毛细管辅助微细电沉积制备金属结构的加工方法,设计并搭建了微细沉积试验平台;
2、仿真研究了金属铜柱结构的微细电沉积制备过程,实现了毛细管辅助微细电沉积制备金属结构,为微细金属3D打印技术奠定了基础;
3、开展了微细金属结构样件的制备工艺试验,优化了加工参数。
工作单位
罗森伯格(昆山)技术有限公司(江苏昆山)
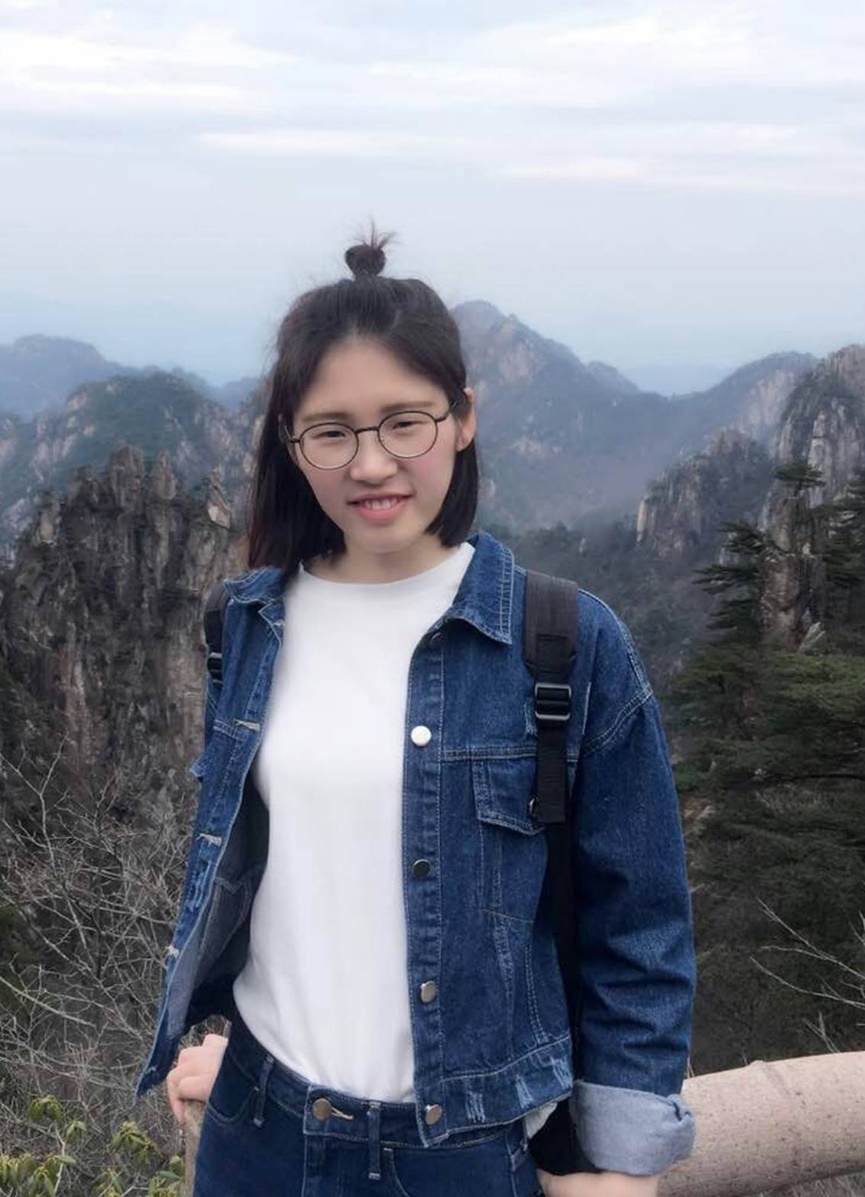
冯秋娜
论文题目
激光熔化沉积成形AlSi10Mg铝合金的工艺与组织性能研究
主要研究
1、研究了激光功率和扫描速度对激光熔化沉积AlSi10Mg合金单道形貌的影响规律;
2、提出了铝合金激光熔化沉积基体热累积的表征方法,建立了简化的数学模型;
3、研究了激光熔化沉积试样的相组成和显微组织演变规律,制备了具有快速凝固致密组织特征的AlSi10Mg合金沉积试样,屈服强度183MPa,显微硬度100~130HV;
4、对AlSi10Mg合金沉积试样进行了“固溶+时效”热处理工艺,屈服强度提高到237MPa
发表论文
[1]冯秋娜,田宗军,梁绘昕,高雪松,肖猛.基体热累积对铝合金激光熔化沉积单道形貌的影响研究[J].应用激光(已录用).
工作单位
江苏恒立液压股份有限公司(江苏常州)
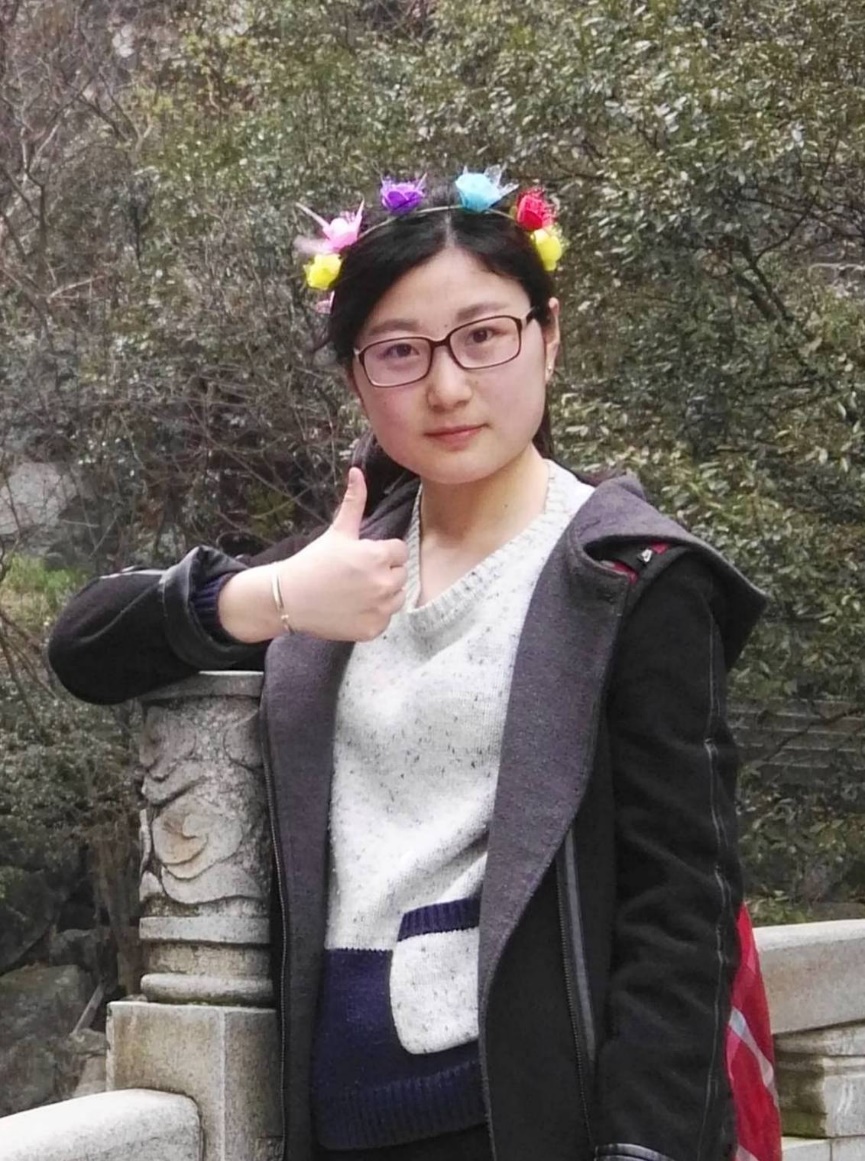
谢娜
论文题目
电磁冲击增强激光熔化沉积的电磁力数值模拟
主要研究
1、针对激光熔化沉积制件中的孔隙、残余应力等缺陷,提出了电磁场与激光熔化沉积过程同步复合的方法;
2、分析了电磁力消减沉积层残余应力机理,从时间、空间两方面研究施加磁场后沉积件所受的电磁力特性,并设计了集磁器;
3、在激光熔化沉积平台上搭建了电磁冲击增强激光熔化沉积装置;
4、进行了不同励磁电流下电磁冲击增强激光熔化沉积的单层单道、多层多道的工艺实验,表明该方法效果良好。
发表论文
[1] Xie N, Zhao J, et al. Simulation and analysis of electromagnetic force in laser melting deposition by electromagnetic impact[J]. Transactions of Nanjing University of Aeronautics and Astronautics.(录用)
[2]孙杰,赵剑峰,谢德巧,谢娜.电磁辅助激光熔化沉积的应力场数值模拟[J].南航学报.(录用)
工作单位
恩斯克中国研发中心(江苏昆山)
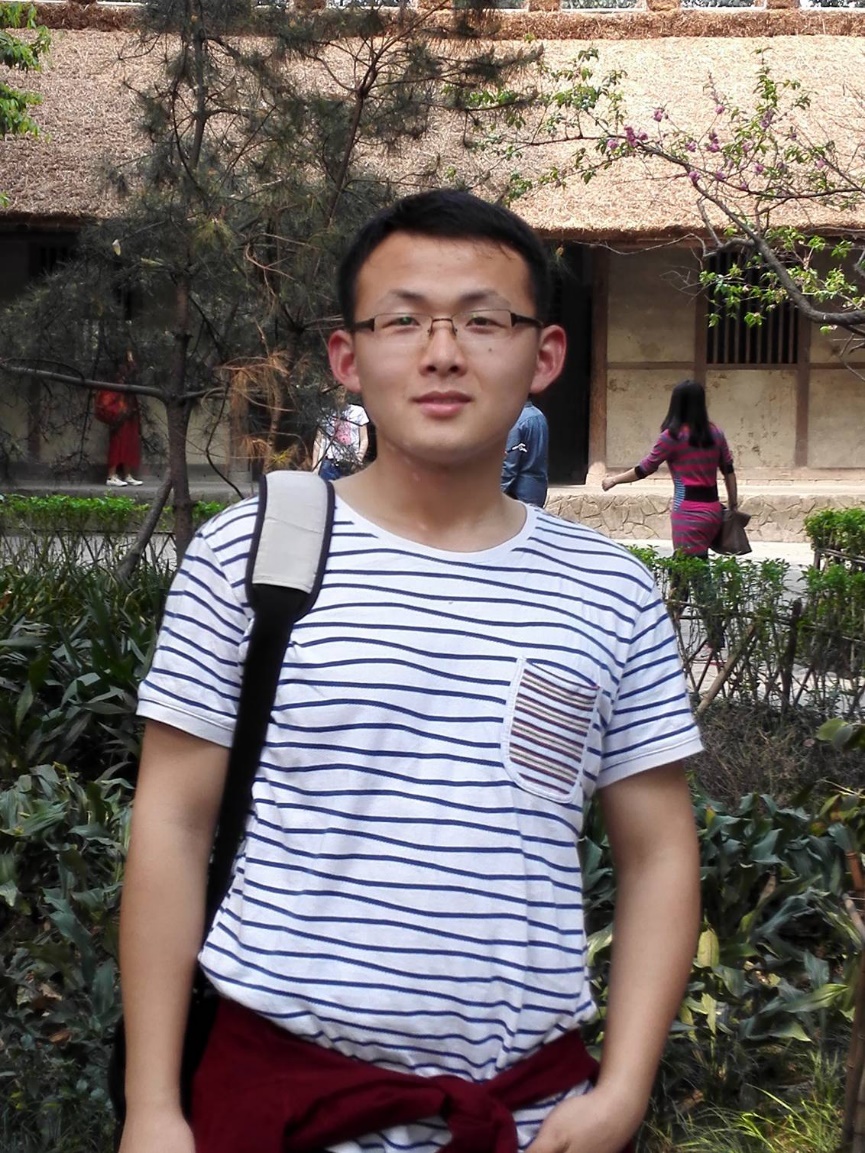
孙杰
论文题目
电磁优化激光熔化沉积的应力场研究
主要研究
1、系统分析了激光熔化沉积残余应力产生的机理以及电磁优化激光熔化沉积的机理;
2、研究了单一激光熔化沉积的残余应力在时间和空间上的分布,分析了固定电磁力对残余应力的影响以及不同电磁力大小的影响规律;
3、开展了激光熔化沉积单道单层试验,制备了金相样件,对制造件内部晶粒组织进行了观察分析;
4、在激光熔化沉积单道单层的基础上,进行了多道单层试验。
发表论文
[1]孙杰,赵剑峰,谢娜,等.脉冲磁场优化激光熔化沉积的应力场数值模拟[J].南京航空航天大学学报.
[2] Xie N, Zhao J, Sun J. Simulation and analysis of electromagnetic force in laser melting deposition by electromagnetic impact[J]. Transactions of Nanjing University of Aeronautics and Astronautics.
工作单位
威卡自动化仪表有限公司(江苏苏州)
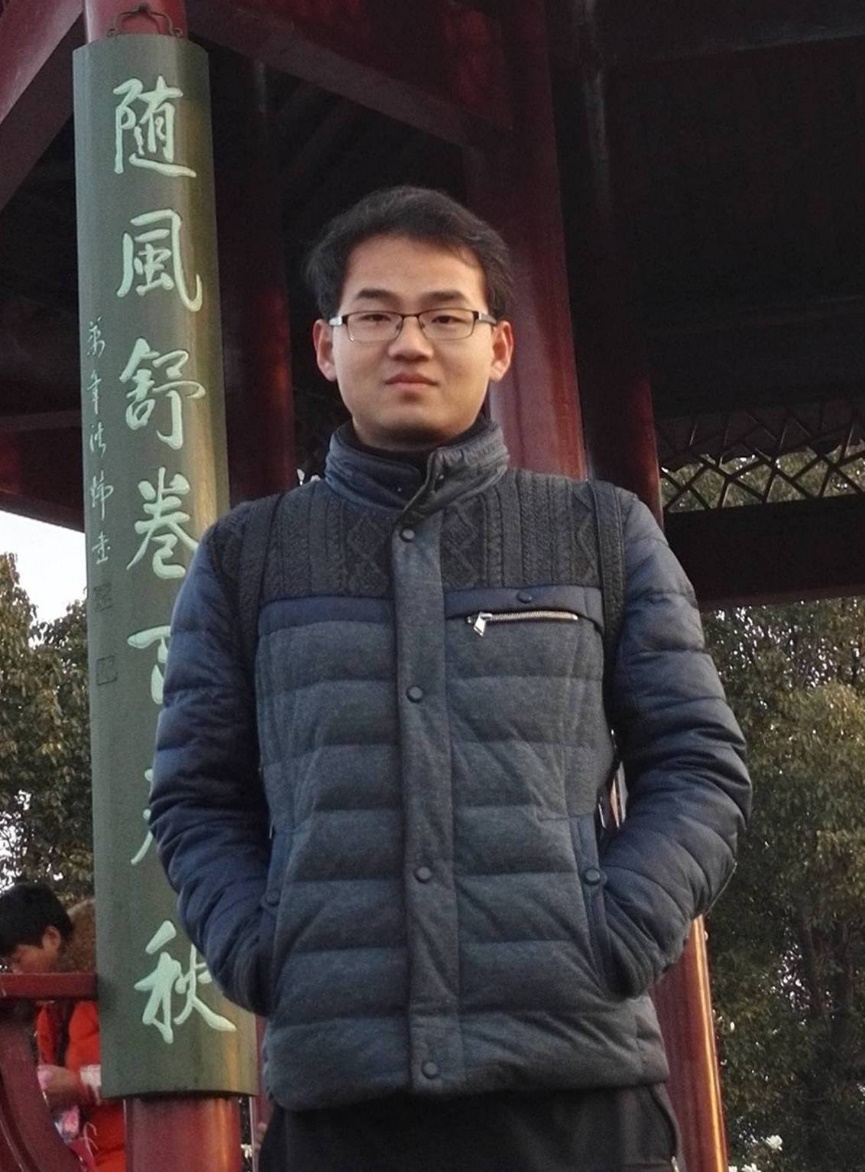
王洛
论文题目
选区激光熔化切片软件的关键技术研究
主要研究
1、研究了切片软件的整体构架及各个模块的功能组成,确定了程序的整体流程,并设计了程序交互界面;
2、开发了STL文件的读取程序,设计了图像交互界面,实现了图形的显示、旋转、平移、缩放、着色和光照等功能;
3、提出了新型的RP技术支撑生成算法,生成了多种类型的支撑结构,并通过软件实现了零件支撑的自动添加;
4、提出了适合本软件的分层切片算法,结合软件可视化功能进行了验证显示。
工作单位
梅特勒-托利多(常州)测量技术有限公司(江苏常州)
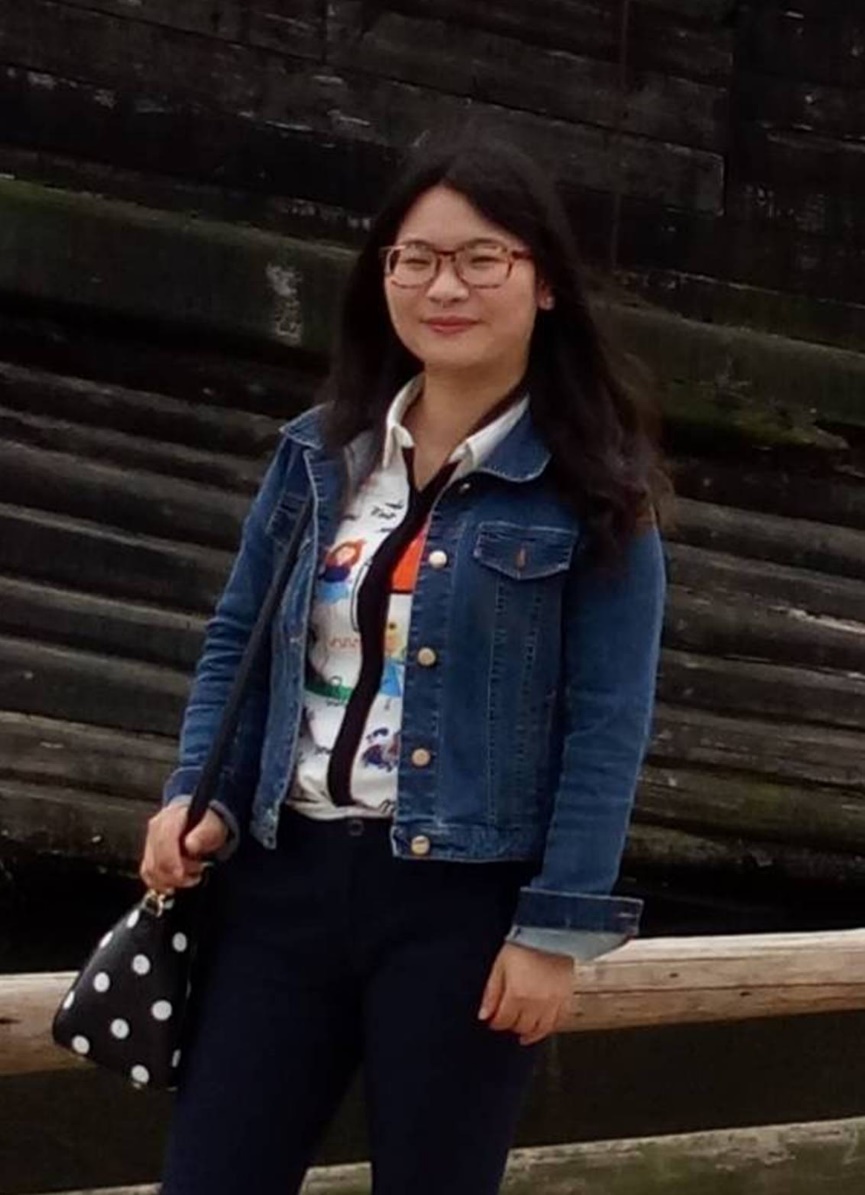
戴露
论文题目
基于固高GT400的振镜扫描及控制系统设计与实现
主要研究
1、研究了振镜控制系统原理及其工作方式,了解了振镜激光扫描的光路系统及扫描的实现过程。构建了振镜激光扫描系统,完成了系统部件的选型。
2、设计了振镜控制系统的硬件架构及其连接方式。研究并编写振镜控制系统驱动程序、激光振镜扫描控制卡程序,设计供粉和铺粉控制系统等。
3、对振镜控制系统进行测试,测试的方法是扫描速度的测试、扫描精度的测试、控制系统稳定性能的测试。结果表明,本论文设计的振镜控制系统、振镜扫描机构及粉床控制系统等稳定性良好、精度较高,满足选择性激光熔化技术的生产要求。
工作单位
南京中科煜宸激光技术有限公司(江苏南京)
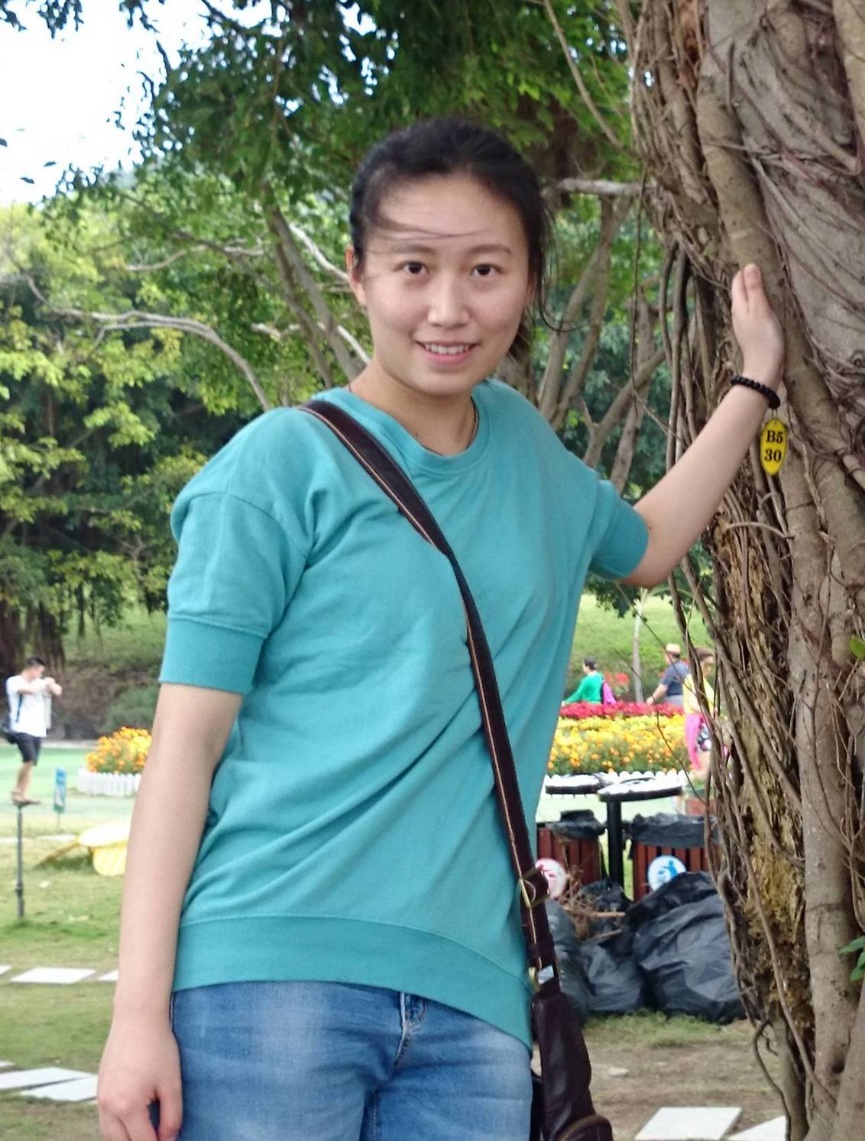
葛梦醒
论文题目
硅晶体定晶向电火花线切割加工损伤层检测研究
主要研究
1、提出了基于X射线回摆曲线法的定晶向单晶硅变质层厚度检测技术,并构建了定晶向单晶硅变质层检测系统;
2、研究了单晶硅电火花线切割加工过程中的蚀除方式,提出了减小加工损伤深度的措施;
3、研究了电火花定晶向线切割加工过程中损伤层的类型、微观形貌结构特征;
4、搭建了喷射电解试验平台,研究了定晶向单晶硅损伤层的去除方法。
发表论文
[1] Mengxing Ge, Zhidong Liu, Lida Shen, et al. Thickness measurement of deterioration layer of monocrystalline silicon by specific crystallographic plane cutting of wire electrical discharge machining[J]. Journal of Materials Science: Materials in Electronics, 2016, 27(9):1-8.(SCI源刊,WOS:000381159800033, IF:1.798)
[2] Mengxing Ge, Zhidong Liu, Haoran Chen, et al. Machining damage of monocrystalline silicon by specific crystallographic plane cutting of wire electrical discharge machining. Journal of Materials Science: Materials in Electronics, 2017.(已录用,SCI源刊,DOI: 10.1007/s10854-017-6562-x,IF:1.798)
工作单位
商飞制造有限公司(上海)
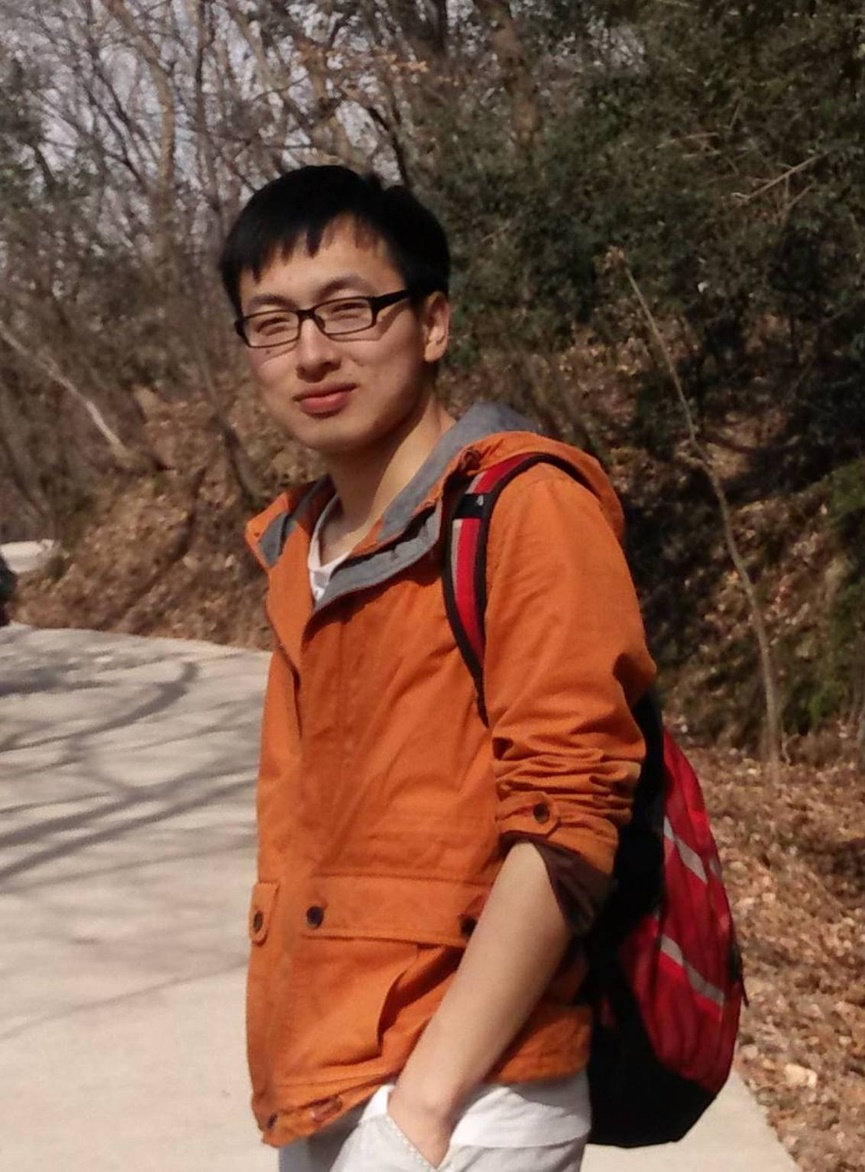
史璟云
论文题目
烧结金刚石电极放电烧蚀磨削复合加工技术研究
主要研究
1、提出了烧结金刚石电极雾化烧蚀磨削复合加工方法,构建了试验系统。
2、提出了压力作为检测信号的伺服控制方法,设计并搭建了整个系统。
3、建立了研究雾化烧蚀磨削复合加工模型。
4、开展了模具钢和高强钢的工艺优化试验。对于模具钢,复合加工的效率是雾化烧蚀的1.88倍,的效率是雾化烧蚀的1.3倍,且复合加工的表面质量要明显好于雾化烧蚀加工的表面
发表论文
[1] Shi Jingyun, Qiu Mngbo, Liu Zhidong, Shen Lida. Discharge ablation grinding machining based on constant pressure feeding[J]. The International Journal of Advanced Manufacturing Technology, 2016: 1-8. (DOI: 10.1007/s00170-016-9714-x, SCI).
[2] Shi Jingyun, Qiu Mngbo, Liu Zhidong, Shen Lida. Discharge ablation grinding machining based on PID control method. The 2016 International Academic Conference for Graduates, NUAA.
[3]邱明波,史璟云,丁成才.烧结金刚石电极放电烧蚀磨削复合加工技术研究[A].中国机械工程学会特种加工分会电火花成形加工技术委员会. 2016年全国电火花成形加工技术研讨会交流文集[C].中国机械工程学会特种加工分会电火花成形加工技术委员会: 2016: 9.
工作单位
中科新松有限公司(上海)
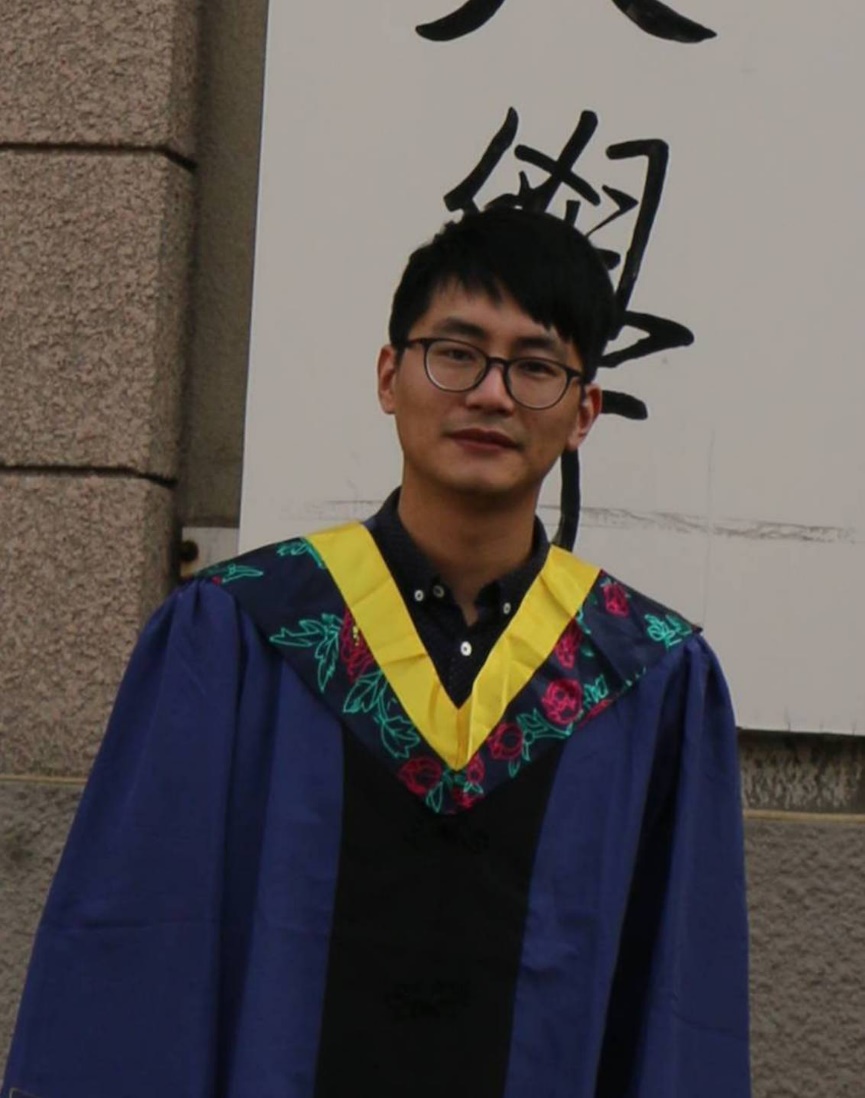
吴勤
论文题目
金刚石线切割走丝系统弯丝及张力控制研究
主要研究
1、研究了金刚石线切割过程中弯丝现象的形成原因,提出了光投影检测法用于金刚石线位置检测,并研制了弯丝检测系统;
2、改造了金刚石线切割机床走丝系统,设计了张力均衡控制系统,张力波动控制在0.6N以内;
3、研究了金刚石线切割张力变化的影响因素,建立了磨粒切割机理模型;
4、进行了多晶硅金刚石线切割工艺试验,高度20mm,直径20mm的多晶硅切割精度控制在0.05mm以内,且切割效率和表面质量均有较大提高。
发表论文
[1] Wu Qin, Liu Zhidong, Zhang Bin, etal. Experimental research on tension balance control of reciprocating winding diamond wire saw. International Journal of Advanced Manufacturing Technology. 2016. (SCI源刊,DOI: 10.1007/s00170-016-9746-2 )
[2] Wu Qin, Liu Zhidong, Shen Lida, etal. Test research on wire deflection detection of a diamond wire saw. International Journal of Advanced Manufacturing Technology. 2016. (SCI源刊,DOI: 10.1007/s00170-016-9787-6 )
工作单位
上海无线电设备研究所(上海)
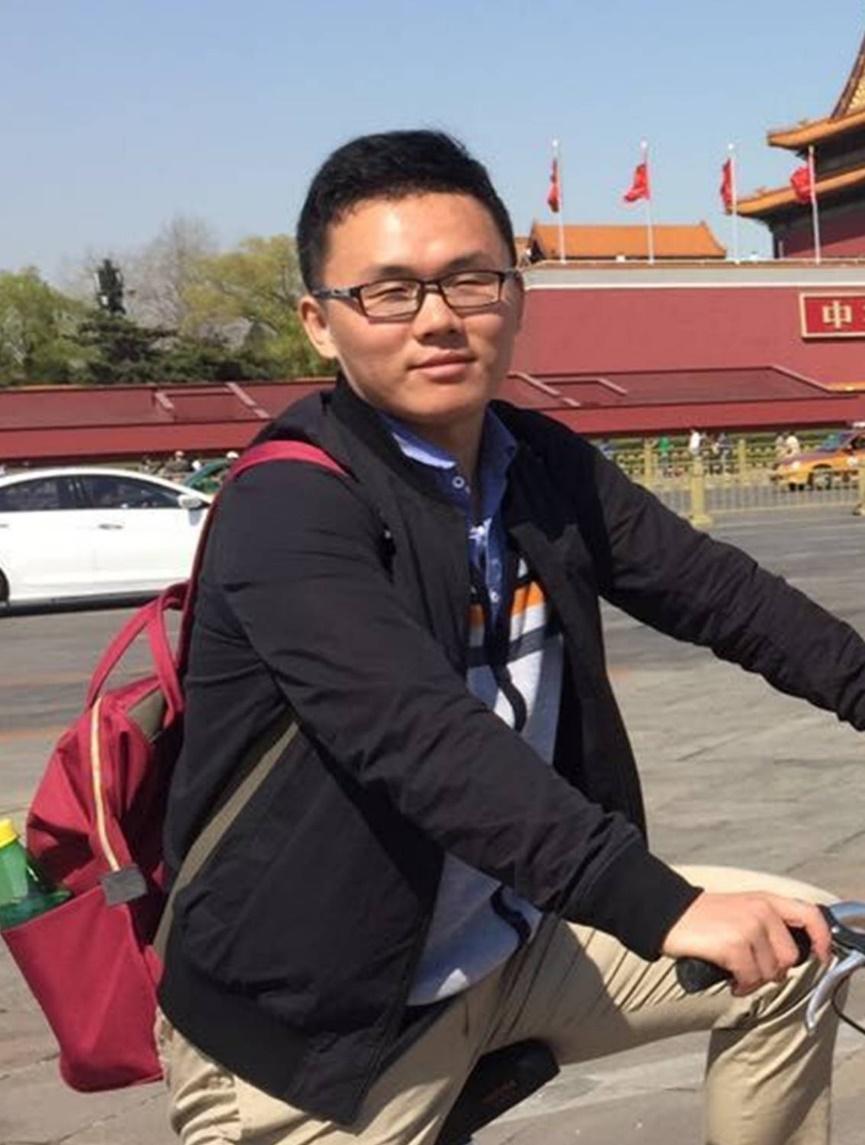
闫昊
论文题目
高速往复走丝电火花线切割电极丝空间形位变化控制研究
主要研究
1、设计制作了恒张力走丝控制系统、防断丝智能导丝机构,实现了电极丝空间形位的有效控制,并进行了对比工艺试验,切割效率提升10%,加工精度提高20%,表面粗糙度值降低20%;
2、设计了电火花线切割大锥度随动导丝机构,改善了大锥度切割的表面质量和加工精度;
3、建立了大厚度多次切割电极丝的受力模型,通过改变走丝速度、修刀补偿量、电极丝直径等条件进行了多次切割试验,“腰鼓度”误差得到了有效控制。
发表论文
[1] Hao Yan, Zhidong Liu, Lingling Li, Chengrang Li, Xiaoxiao He. Large taper mechanism of HS-WEDM . International Journal of Advanced Manufacturing Technology (SCI:IF1.568)
[2]闫昊,刘志东,李明明.往复走丝电火花线切割工作介质过滤方式研究.全国电火花线切割加工技术研讨会论文集.盐城, 2016: 53-61.
[3]张旭东,闫昊.往复走丝无人化工作液供给和处理系统.全国电火花线切割加工技术研讨会论文集.盐城, 2016: 41-46.
工作单位
AO.史密斯热水器(中国)
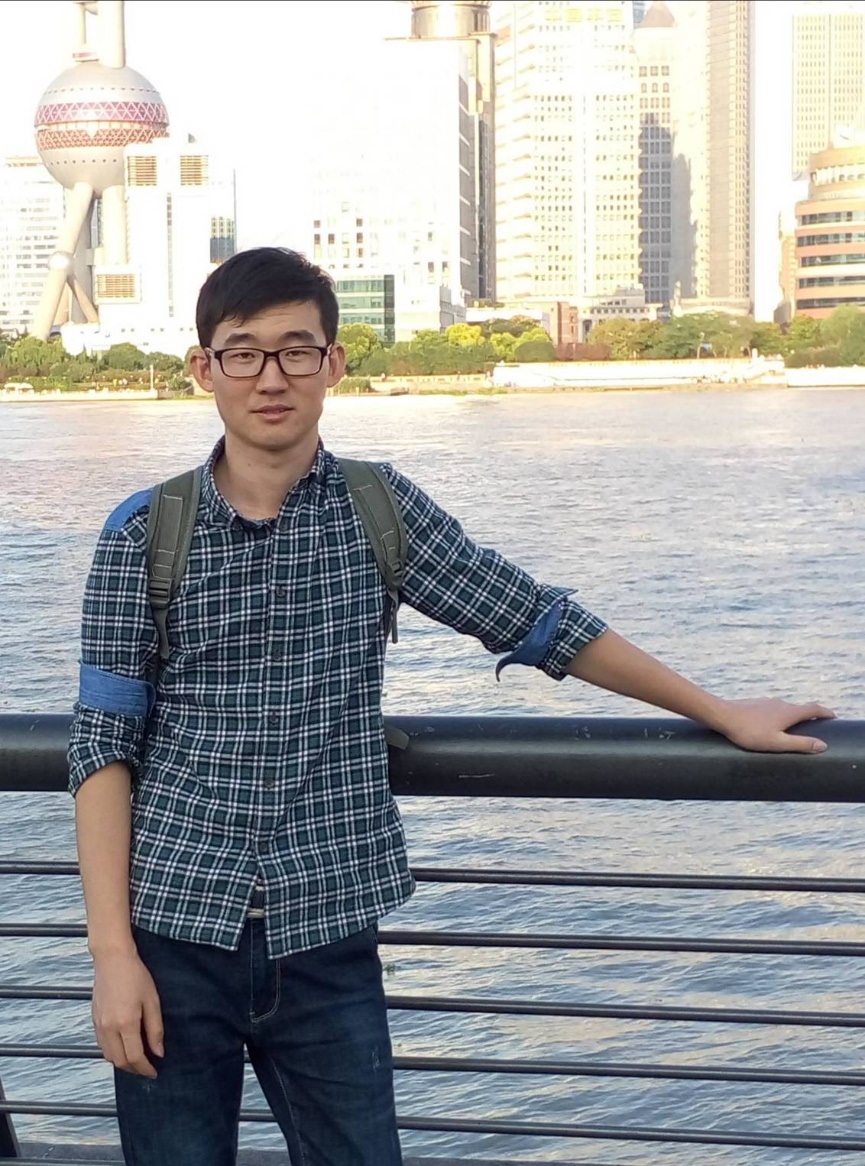
张超
论文题目
冷电极电火花加工温度控制及蚀除机理研究
主要研究
1、基于半导体peltier效应设计制造了冷电极结构,以DSP为核心设计了温度检测和控制系统;
2、分析了电极温度对极间放电通道和放电间隙的影响,建立了极间放电通道模型和放电间隙模型;
3、研究了电极温度对电蚀坑形貌的影响规律,进行了不同电极温度下的单脉冲放电验证试验;
4、进行了冷电极与常规电极加工钛合金对比试验,冷电极加工电极损耗降低了19.5%,材料蚀除率提高了8%,表面粗糙度降低了14.14%。
发表论文
[1] Zhang Chao, Qiu Mingbo, Yan Jing, Han Yunxiao. Influence of electrode temperature on cool electrode EDM. 2016 International Academic Conference for Graduates, NUAA. 2016: 85-89.
[2] Zhang Chao, Qiu Mingbo, Yan Jing, Han Yunxiao. Influence of electrode temperature on electric erosion pit morphology during cool electrode EDM. Journal of Advanced Manufacturing Technology. 2016.(SCI源刊,在审)
工作单位
常州博瑞电力自动化设备有限公司(江苏常州)
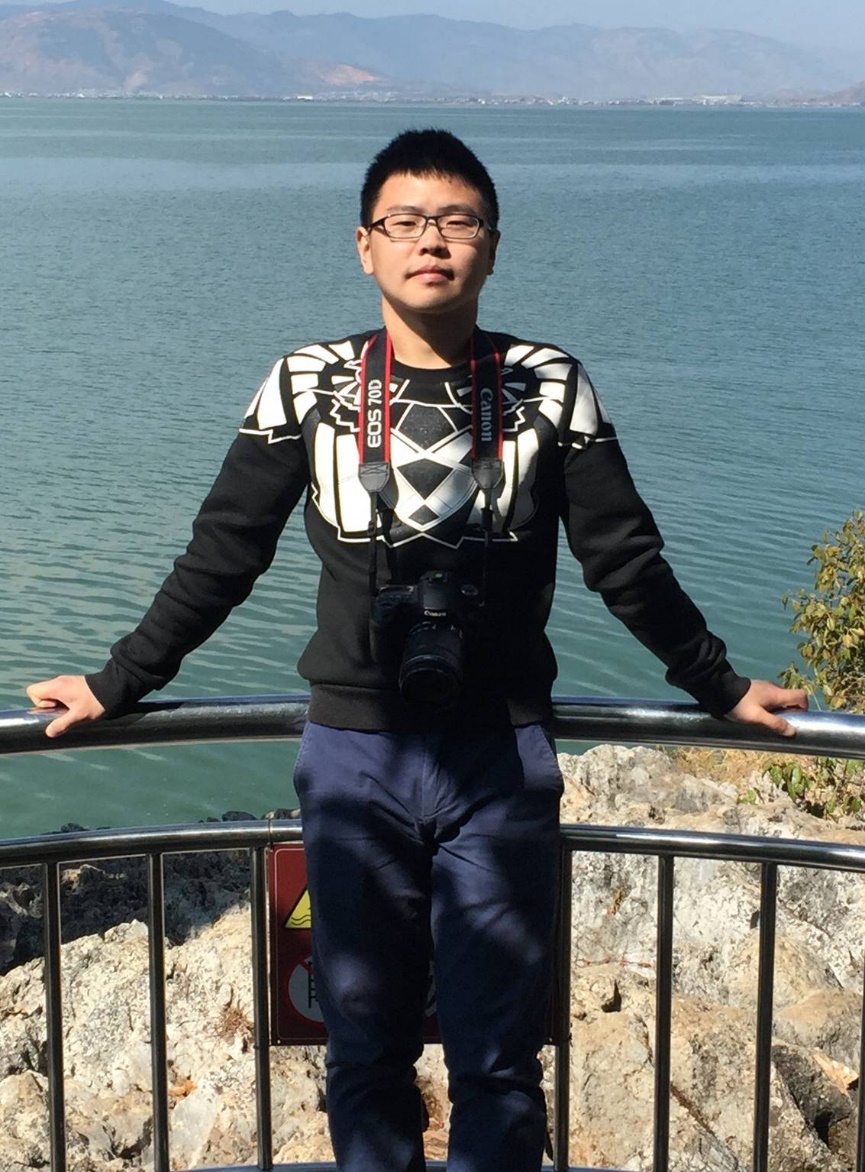
贺笑笑
论文题目
硅晶体电火花线切割伺服控制与工艺研究
主要研究
1、研究了金属放电和硅晶体放电差异,提出了基于放电概率检测的硅晶体电火花线切割PID伺服控制法;
2、设计搭建了单脉冲微细放电加工试验平台,通过单脉冲试验研究了提高脉冲利用效率的方法;
3、以FPGA为核心设计改造了现有电火花线切割伺服控制系统,开展了变目标概率、变能量和拐角切割工艺试验。
发表论文
[1]贺笑笑,刘志东等.基于放电概率检测的硅晶体电火花线切割伺服控制研究[J].电加工与模具.(中文核心)
[2] Yan H, Liu ZD, Li LL, Li CR, He XX. Large taper mechanism of HS-WEDM[J]. International Journal of Advanced Manufacturing Technology, 2016:1-9. (SCI源刊,收录)
工作单位
宝时得科技(中国)有限公司(江苏苏州)
编辑:邱明波